D. Post War Production
Aswar time production ended, Acklin expanded its domestic production rapidly. The influx of experienced workers and a growing demand
for consumer goods such as washing machines, refrigerators, and air conditions, caused rapid expansion at Acklin. In 1947 there
were 475 employees, double the amount employed there three years prior, during the peak days of the shell line, and nearly as many
as during the period of prosperity in the late 1920's.
Shortly after the war Acklin began to take orders from the Tecumseh Products Corporation of Tecumseh, Michigan. A leader in the
compressor industry, Tecumseh had Acklin stamping compressor housings for use in the rapidly growing fields refrigerators, air
conditioners, and other cooling systems. Acklin also took large orders for parts from the Bendix Washing Machine Company of South
Bend, Indiana.
During this period Acklin was actively involved in seeking out new orders in an effort to supplement and maintain production levels.
The rapidly expanding economy, particularly for domestic consumer goods created a great deal of competition between various firms
for the larger, more steady jobs.
When the Korean War broke out in the early 1950's Acklin hoped to claim a large number of defense contracts, as they had during
World War II. However things didn't work out quite like they expected. During 1951 the Acklin Press reported that 95% of the
orders placed by Acklin were for defense or war materials. Very few of these were produced however and most Acklin work remained
civilian.
There was also a great deal of pressure placed upon the steel supply with much of the higher quality steel going to the automotive
industry which was producing automobiles at a record rate. Some companies when placing a stamping order with Acklin would provide
their own steel as well, but this was a fairly rare occurrence. Occasional labor disputes in the coal mining and steel industries
would also hurt supply, forcing prices up. Or, if strikes seemed imminent but never materialized, Acklin was often left with an
overstock of steel which would force up production costs.
These pressures created the need for dedicated and concentrated effort on quality control for the jobs already received and a
certain degree of fluctuation of employees. The air conditioning business itself was fairly cyclical with production peaking in
the late winter months in an effort to prepare for summer demand. Acklin had a policy for these inevitable summer layoffs that was
based on seniority and rank, those that were laid off were placed on a list and they were the first individuals hired when
production demands increased in the fall. Despite these fluctuations Acklin remained one of the largest and most productive
stamping plants in the Toledo area.
In1947 Acklin's plant was 115,000 square feet in size, housing 150 presses and using 18,000 tons of steel per year. Thirty-five
percent of Acklin's business still relied on the automotive industry, supplying parts used in Willys-Overland, Studebaker,
Chrysler and GM cars. Another 35% of Acklin's business, approximately 4,000 units per day, went into the production of compressors
and compressor parts used in refrigeration and air conditioning by a variety of companies including Michigan based Tecumseh
Products. Acklin also stamped parts for household appliances -- washing machines, vacuum cleaners, and air conditioning,
production that comprised 20% of Acklin's output. The remaining 10% was invested in the production of agricultural and other
miscellaneous stampings.
Tecumseh wasn't the only company Acklin stamped compressor housings for, they also produced parts used in compressors assembled by
General Electric and Westinghouse, but Tecumseh Products became an increasingly important source of business. In January of 1949,
rather than lose Tecumseh as a customer, Acklin cut their prices on housings by 14 cents per unit, representing a significant loss
of profit.
In1950 Acklin began the production of pistons used in the assembly of compressors for Tecumseh Products. The pistons were designed
through a joint effort of both Acklin and Tecumseh engineers and this new job order provided 25 new jobs, mainly on the small
press lines. This and other similar ventures were a result of the growing co-operation and co-dependence the two companies were
quickly forming.
Inlate 1951 Acklin was still searching widely for outside orders to increase their production and provide enough work to maintain
the number of employees, but layoffs were inevitable. Several parts Acklin was producing they had underbid on in order to receive
the order and the work involved, but were losing money on fairly rapidly. Steel was scarce and workers were uneasy about job
security. Finding themselves in an increasingly complex and chaotic industrial marketplace they began to attach increasing
importance to Tecumseh's steady business.
|
Producing parts for Bock Laundry,1948
Aerial view of Acklin Stamping, 1940s.
Acklin stamped push mower. Photo 1940s.
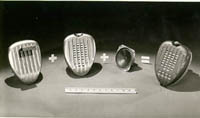 Drive-In movie speakers, Acklin, c. 1940s-1950s.
Bendix washing machine parts, late 1940s.
Piston stamped for Tecumseh Products, 1950s.
|